EPDM Single Ply membrane
- carissa184
- Aug 3, 2016
- 3 min read
Updated: Sep 20, 2021
EPDM single-ply membranes have been the commercial roofing industry’s material of choice for nearly half a century, and Carlisle has been defining the standard since the beginning. Today, Carlisle SynTec offers the most high-performance, energy-efficient, sustainable and innovative line of EPDM membranes and accessories on the market. From Factory-Applied Tape (FAT®) for stronger, more dependable seams to the industry’s only ENERGY-STAR®-qualified EPDM membrane, no one offers the versatility and performance like Carlisle. So when you need a sustainable, long-lasting rooftop, look no further than the single-ply membrane with nearly a half-century track record of performance and durability...Carlisle EPDM.
An ENERGY STAR®-qualified EPDM membrane, Carlisle’s Sure-White EPDM is an ideal solution for building owners looking to reduce air conditioning costs without compromising roof system performance or durability. Sure-White membranes feature the same material characteristics as Carlisle’s standard EPDM, have over 20 years of proven field performance, are CRRC-certified and help contribute toward LEED® credit requirements.
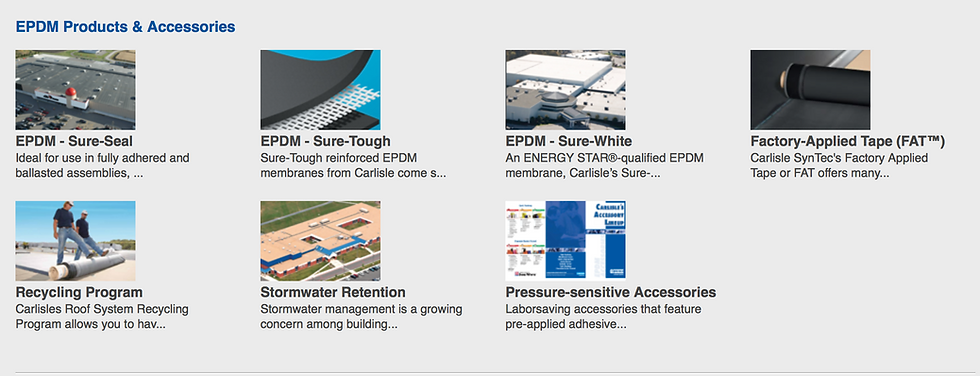
Why Single-Ply?
A closer look at non-asphalt-based single-ply roof systems reveals the benefits, costs, and application methods
Careful consideration should be taken so that the proper number of fasteners is used in mechanically attached single-ply roofing applications. An insufficient number of fasteners could result in blow-off.
If you’ve sipped the alphabet soup of single-ply roofing systems, then you probably have a taste for their characteristics and advantages. However, if you have yet to experience membranes such as TPO, PVC, EPDM, or Hypalon, get ready – Buildings is dishing out everything from the basics and beyond to help you better understand these non-asphalt-based systems.
Single-ply roofing membranes have grown in popularity over the past 30 years, and due to their flexibility, relative ease of installation, and competitive price, it’s no wonder that building owners and facilities professionals are interested. According to the Waltham, MA-based Single Ply Roofing Industry (SPRI), a commercial roofing industry association, one of the benefits to single-ply membranes is their production; they are “manufactured in a factory to strict quality control requirements that minimize the risk inherent in built-up systems.” This consistency in the quality of the products is undeniably one of its selling points.
But owners aren’t the only ones hailing the praises of these membranes. “I think most roofing contractors [and] roofers would generally find single-ply roofing easier to install, neater, and cleaner to work with. For example, with a single-ply roof, there’s not a need for one of these big kettles to heat up bitumen, so it’s cleaner,” says Vincent McPartland, vice president, sales and marketing, Stevens Roofing Systems, Holyoke, MA. Installation of a single-ply membrane is often faster as well.
At the same time that single-ply membranes were gaining market share in the United States, concerns for the environment and an emphasis on energy conservation became paramount. Single-ply membranes offered a solution – a very cool one. Light-colored, reflective roof surfaces could offer building occupants a significant reduction in energy use, points toward a U.S. Green Building Council LEED™ building certification, as well as the potential to downsize HVAC equipment. Additionally, single-ply membranes offer a lightweight solution that can accommodate the sometimes unconventional roof designs of modern architecture.
After spelling out so many wonderful attributes, you may be wondering what you’re giving up with a single-ply membrane. The answer is in the question. Because these systems are only one ply (as their name suggests), you’re sacrificing the security of a redundant system. As with any installed roof, caution should be taken to avoid punctures and damage. “That’s probably the biggest drawback in some people’s eyes,” says Tim McFarland, technical director, Mule-Hide Products Co. Inc., Beloit, WI.
Comments